Overview of SHIMADZU Automotive Technology Webinars for Weight Reduction
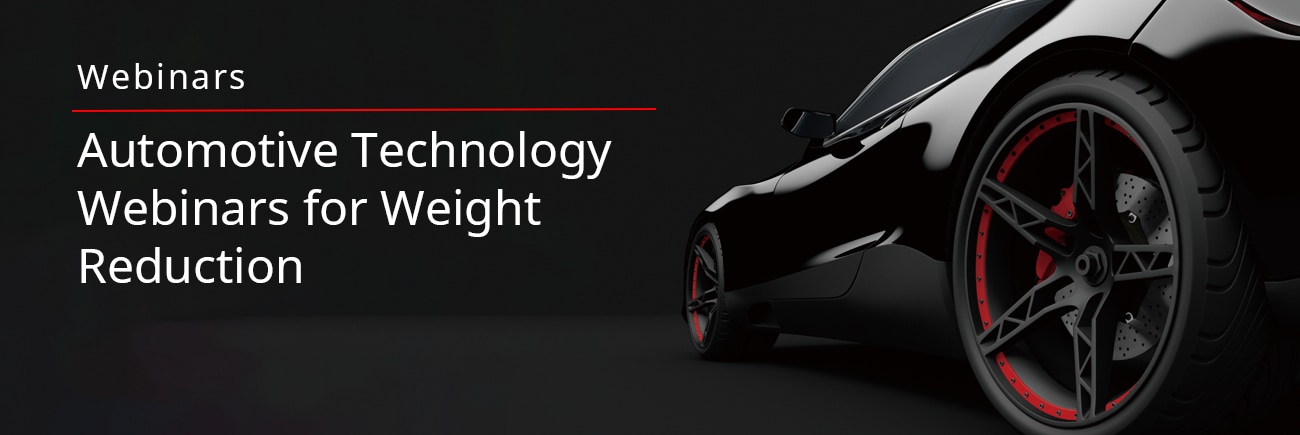
What’s New
- 2022.03.24
Registration is closed for Weight Reduction Using Composite Materials, Basic Course.
Purpose of Automotive Technology Webinars for Weight Reduction
To reduce the environmental impact of automobiles, it is important to improve their fuel efficiency, and vehicle weight reduction is one way of achieving this. In recent years, the adoption of CASE has become a key for automobile development. As a result, the weight of automobiles has been increasing due to the increase in the number of ECU units, the number of sensors, and the weight of batteries. Thus weight reduction is essential for CASE. Furthermore, to achieve such reductions, a combination of technologies is required. Various technologies are being developed, including the use of composite materials such as GFRP, CFRP, CFRTP, and CNF reinforced plastics, press working technology for new metallic materials such as high-tensile strength steel and aluminum alloys, analysis technology to improve design accuracy, multi-material technology, and 3D printing technology, which is expected to be used for future automotive structure development.
The SHIMADZU Automotive Technology Webinars for Weight Reduction provide support for achieving weight reduction by introducing detailed information about the latest technologies for each of the technical themes below and the evaluation technologies they require.
Weight Reduction Using Composite Materials, Basic Course
-
- Dates: Mar. 24th 2 pm-Mar. 25th 2 pm EST
-
Register Closed
-
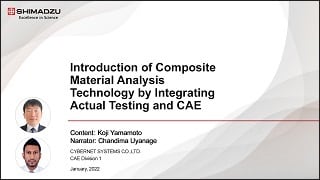
Special Invited Lecture
Introduction of Composite Material Analysis Technology by Integrating Actual Testing and CAE
Presenter
Koji Yamamoto and Chandima Uyanage, CYBERNET SYSTEMS CO., LTD.
Since composite materials have high specific strength and specific rigidity, they are expected to contribute to the weight reduction of automobile structures. However, since fiber-based composite materials are anisotropic, the stresses they will be subjected to during use must be examined in advance, and the parts must be carefully designed so that the fibers are oriented in the direction that requires the highest rigidity. In addition, because the materials are expensive, it is important to reduce the number of prototypes as much as possible. CAE is an attractive technology that can solve these problems.
Therefore, this lecture introduces the latest CAE analysis technology focusing on weight reduction design.
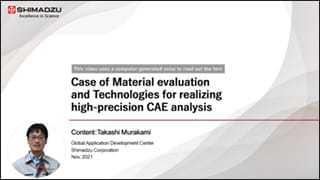
Case of Material evaluation and Technologies for realizing high-precision CAE analysis
Presenter
Takeshi Murakami, Shimadzu Corporation Global Application Development Center
There is a demand for automobile weight reduction in order to reduce the environmental impact, and the use of composite materials such as CFRP has begun. Unlike conventional materials, composite materials show complicated fracture behavior depending on the stress loading direction due to the complexity of the internal structure. As a result, high technical capabilities are required to establish a highly accurate structural analysis model when designing using composite materials.
In this presentation, we will introduce an example of verifying the validity of the tensile behavior of thermoplastic CFRP by comparing actual tests and numerical analysis results. In addition, we introduce effective test solutions for realizing high-precision CAE analysis, including examples of CFRP evaluation using the multi-channel strain measurement function and moire measurement system installed in the latest material testing machines.
Weight Reduction Using Composite Materials, Advanced Course
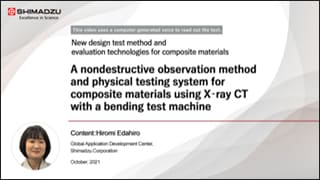
New design test method and evaluation technologies for composite materials
- A nondestructive observation method and physical testing system for composite materials using X-ray CT with a bending test machine -
Presenter
Masami Edahiro, Shimadzu Corporation Global Application Development Center
In areas of transportation such as automobiles and aircraft, weight reduction is being achieved by using composite materials such as CFRP to improve fuel efficiency. However, unlike conventional materials, composite materials have a complicated internal structure, so it has been difficult to observe their actual fracture behavior. In this presentation, we introduce an example of observing fracture behavior using a combination of a testing machine and an X-ray CT system.
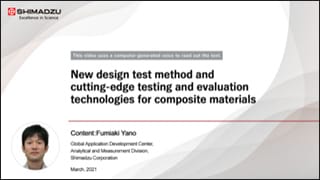
New design test method and cutting-edge testing and evaluation technologies for composite materials
Presenter
Fumiaki Yano, Shimadzu Corporation Global Application Development Center
In areas of transportation such as automobiles and aircraft, there are increasing opportunities to use composite materials to achieve weight reduction and low fuel consumption. However, when considering actual usage conditions, important evaluations must be made. These include not only static tests but also impact tests under various temperature conditions. In this presentation, we introduce the benefits of impact testing in composite materials and give test examples.
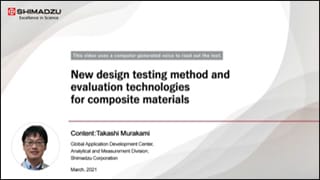
New design testing method and evaluation technologies for composite materials
Presenter
Takeshi Murakami, Shimadzu Corporation Global Application Development Center
CFRP is expected to be adoped to reduce weight for the purpose of improving fuel efficiency in automobiles and aircraft. Unlike conventional materials, composite materials exhibit complex fracture behavior depending on the stress loading direction due to the complexity of their internal structure. This presentation, introduces a linear/nonlinear behavior evaluation test system for inter-laminar/out-of-plane shear testing to establish a high-precision CAE analysis model for investigating the bending and axial crushing behavior of composite materials. In addition, we describe an example of comparing and verifying the validity of the test system and the test method using actual test data and CAE analysis.
Weight Reduction Using New Press Forming Technology
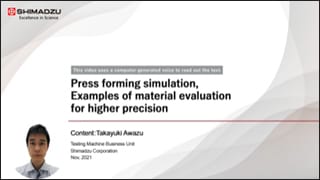
Press forming simulation,
Examples of material evaluation for higher precision
Presenter
Takayuki Awazu, Shimadzu Corporation Testing machine business unit
There is a demand for weight reduction in automobiles to reduce their environmental impact, and high-tensile steel plates are attracting attention as one solution. This presentation, introduces an example of a high accuracy molding simulation using r-value and Bauschinger effect data and test methods as an illustration of an effective method for realizing high-precision CAE analysis when designing press-formed parts.