Flexural Testing of CFRP Boards
Standard No. JIS K 7074: 1988
Carbon fiber reinforced plastic (CFRP) is a composite material with excellent relative strength. This plastic was quickly adopted in the aviation and space sectors, and has contributed significantly to reducing fuselage weight. Initially, this plastic was only used for partial replacement of metal materials. In the latest aircraft, however, composite materials, primarily CFRP, represent 50 % of the fuselage weight. Improved productivity and reduced costs are expected due to subsequent technical developments, and it can be expected that this plastic will also become popular as a main material in automobile frames. Here, a CFRP cloth was subjected to a flexural testing using a precision universal tester in order to evaluate the strength of the material.
Measurements and Jigs
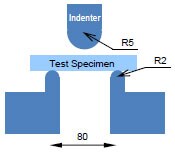
In flexural testing specified in JIS K7074, a loading edge radius of 5 mm, and a
support radius of 2 mm are specified. The specimen standard dimensions are
specified as follows:
Length = 100 mm ± 1 mm
Width = 15 mm ± 0.2 mm
Thickness = 2 mm ± 0.4 mm
For tests performed using a specimen with the standard dimensions, the span between supports (L) will be 80 mm ± 0.2 mm. When TRAPEZIUM software is used, the flexural stress can be automatically calculated and plotted in a graph from the test force and the specimen dimensions. The flexural strength and other characteristic values can also be obtained from a few simple operations.
Measurement Results
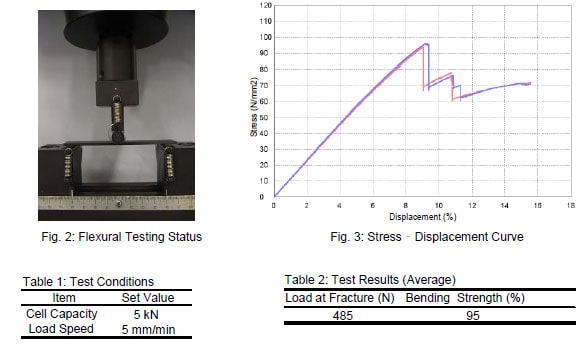
CFRP Flexural Testing System
Tester: AG-Xplus
Load Cell: 5 kN
Test Jig: Three-point bending test jig for plastics
Software: TRAPEZIUM X (Single)
- A high-precision load cell is adopted. (The high-precision type is class 0.5; the standard-precision type is class 1.)
Accuracy is guaranteed over a wide range, from 1/1000 to 1/1 of the load cell capacity. This supports highly reliable test evaluations. - Crosshead speed range
Tests can be performed over a wide range from 0.0005 mm/min to 1,500 mm/min. - High-speed sampling
Ultrafast sampling, as fast as 0.2 msec. Sudden changes in test force, such as when brittle materials fracture, can be assessed. - TRAPEZIUM X operational software
Designed for intuitive operation, this software offers excellent convenience and user friendliness. - Smart controller
Real-time test force and position data is readily confirmed, and the manual dial can be used for fine adjustments to jig positioning. - Optional Test Devices
A variety of tests can be conducted by switching between an abundance of jigs in the lineup.