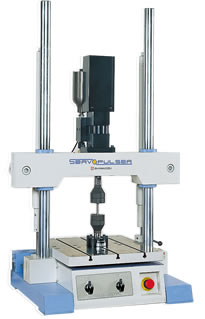
EHF-L Series
INDUSTRIA
Engineering Materials, Automotive
PALABRA CLAVE
Composites, Additive Manufacturing, Steels, Light Metals
INTRODUCCIÓN SERVICIO Y PRODUCTOS
EHF-L Series, EHF-U Series, HITS-X Series, USF-2000A, AGX-V2 Series, DUH-210/DUH-210S, MCT Series, Hyper Vision HPV-X2
Materials testing technology provides the data and decision basis for the development, design and manufacture of operationally reliable high-performance products for all sectors of industry. Successful material selection, quality control, component monitoring and failure analysis are based on the correct determination of chemical composition, microstructure and defect structure, material properties and damage evolution, complemented by powerful modelling and simulation methods. In addition to material qualification and manufacturing optimisation, the identification and separation of fundamental deformation and damage mechanisms, structural integrity and service life prediction is of great importance.
The Department of Materials Test Engineering (WPT) of TU Dortmund University has been headed by Prof. Dr. Frank Walther since the establishment in December 2010.
*Los afiliados y los títulos del entrevistado están actualizados al momento del informe.
TU Dortmund University, Department of Materials Test Engineering (WPT)
URL
https://wpt.mb.tu-dortmund.de/en/
Can you discuss the analysis carried out in your labs and your involvement in the activities, for what purpose are you using Shimadzu Testing machine(TM)?
In the field of materials science and engineering, we carry out metallography and microstructural analysis (light, electron and X-ray) and fatigue experiments (low to very high cycle fatigue – LCF to VHCF, high temperature and corrosion fatigue), apply physical measurement techniques for condition monitoring, develop methods for calculation of damage evolution and (residual) lifetime, and practice mechanism-oriented modeling and simulation of materials behavior and failure analysis.
The first Shimadzu equipment WPT used was a tensile tester – establishing the maximum load a material can withstand before failure. Yield and tensile strengths in dependence of the strain rate are important parameters for evaluating reliability, providing a basis for design of components, particularly when they will be prone to extreme loading. However, in some applications, the load amount that a material can bear quasi-statically is not as relevant as the number of cycles with a specific load or deformation. Fatigue testing measures the material’s resilience to multiple cycles of loading, and has been a key aspect of WPT research. Fatigue testing in the LCF to HCF regime (servopulser) until VHCF regime (ultrasonic systems) is also a core strength of Shimadzu’s product portfolio, like analytical tools which allow real-time characterization of systems under test. Energy-dispersive X-ray (EDX) analysis probes the electromagnetic spectrum of different elements for chemical characterization. Another widely used tool is Fourier transform infrared (FTIR) spectroscopy, which can identify changes in chemical composition of polymers to track aging.
Destructive testing only – conventional tensile and fatigue testing – is not expedient. It is necessary to couple this testing with advanced non-destructive testing and competences in analytical fields. The multitude of characterization methods includes process- and product-optimized strain, temperature, resistance, magnetic, optical and acoustic measurement techniques as well as correlated light and scanning electron microscopy (SEM) and computed tomography (CT), including modules for in-situ loading. The combination of destructive and non-destructive inspection (NDI) methods provides important information about the physics of processing and operating and their effect on changes in microstructure, evolution of deformation and damage on different scales, crack initiation and propagation.
On the basis of combined investigation strategies, we can predict the performance and lifetime of implants under operating conditions and assess how long things will last in the body. To describe the damage tolerance in additive manufactured (AM) structures, we determine the complete process and separate the mechanisms in order to enable lifetime optimization in applications oriented for transportation industries, and combine the knowledge matrix with process chain parameters and service loading spectra, especially low and elevated temperatures. This coupled research approach is applicable across all WPT research groups.
We tested the fatigue behavior of the aluminum wrought alloy EN AW-6060 using a continuous load increase testing procedure for various common manufacturing techniques: thread cutting, thread forming and thread milling in rolled flat specimens compared to extruded bulk materials. Shimadzu’s EDX-720-P energy-dispersive X-ray fluorescence spectrometer was used to detect the chemical composition of processed alloys, and the grain sizes were determined by counting the number of grain boundary intercepts in micrographs.
Once again, key to tensile testing was Shimadzu’s AG-X-plus testing machine and TRViewX integrated high-accuracy video extensometer for strain measurements. For fatigue testing, the Shimadzu EHF servopulser systems are available. Additionally, chambers for superimposed temperature and humidity conditions to be integrated in the testing machines allow the validation of results. To summarize, we pursue two main goals: The basic understanding of deformation and damage mechanisms and evolution under service-relevant conditions for use in the context of lightweight construction and energy efficiency, and the development of new linked destructive, non-destructive and analytical investigation strategies for the reduction of testing time and costs, and instrumented microstructural-mechanical in-situ testing.
Why do you choose Shimadzu TM, and why do you think Shimadzu has an advantage in the market?
Shimadzu manufactures analysis and testing systems for industry and academia and is open to technical adaptations and further developments, like a partner in science. Therefore, an open-minded exchange without references to standard configurations is appreciated. Discussions at a high technical level are facilitated by the training and knowledge of persons involved. Accordingly, an important decision criterion is the quality of advice. No less important is the technical quality – hardware and software – of analysis and testing systems. Despite the scope of functions, user-friendliness and intuitive operation are important, especially in academia, since several people (students, PhD students) will operate the systems for reaching their scientific goals.
Several projects rely on Shimadzu equipment, e.g. applications for transport, power plant and bridge engineering remain a key focus, while a main aspect is energy. Now we have new demands for energy and cost savings, leading to higher requirements to accommodate social obligations, as well as for lighter and safer constructions. These energy considerations are also significant in alloyed metals and composites research. We investigate diverse low- and high-alloyed steels and lightweight metals – conventionally and additively manufactured – as well as polymer-based and renewable material systems, also as hybrid structures. The combination of the HITS-T/P10 high-speed tensile and compression testing system with the HPV-X2 high-speed camera is unique for the assessment of deformation and failure mechanisms at high strain rates, i.e. testing speed until 20 m/s = 72 km/h. This enables the correlation of digital images of the process to capture the evolution of high-speed deformation and damage tolerance on a scientific level.
What criteria did you use to select your system, and which futures of Shimadzu products impressed you?
Systems are selected according to the price/performance ratio, i.e. in case of identical scope of offer and quality of production, generally the most economical supplier has to be considered. Requirements and specifications as well as performance features, compatibility with existing equipment and any follow-up costs during operation are to be included in the decision process. The quality of consultation, discussion and installation is crucial, based on a good understanding of the system and its details. Furthermore, the systems are characterized by high reliability and accuracy, safety and user-friendliness. The after-sales contact with product manager and specialist creates the basis for further function and accessory developments.
The multi-material design and development of heterogeneous materials with graded structures introduce more complex loading histories and the need to monitor an increasing number of parameters contactless for the optimization of local properties. The WPT team aims to predict the interactions of heterogeneous materials based on local microstructures and deformation/failure mechanisms identified through linked destructive, non-destructive and analytical investigations. In summary, we are convinced by product quality, technical maturity, and service capabilities.
Was the method development easy on Shimadzu, and how do you look at Shimadzu with respect to technology, product and support?
The ultrasonic fatigue testing system USF-2000A allows fatigue testing at ultrasonic frequencies of 20 kHz. This makes it possible to test the material’s response until 1E7 cycles in 10 minutes and until 1E10 cycles over 6 days. If the cycle is from a stress in one direction to an equal stress in opposite direction, the load ratio is -1. However, this does not always reflect the stress materials are subjected to during operation. The USF-2000A in standard configuration is qualified for fully-reversed loading. To accomplish requirements with superimposed mean loads, the new USF-2000A in mean stress configuration was developed by Shimadzu.
Another development centered around the high-speed camera HPV-X2, which sheds light on deformation and failure of materials under high strain rates at the high-speed testing system HITS-T/P 10. This approach required a demanding image capture rate – 2,000,000 frames per second for CFRPs. In tests, a signal-processing bottleneck in the image acquisition speeds when converting the light incident on the photodiode from an analogue electrical charge to a digital signal was identified. CFRPs have a tensile strength more than around 20 times higher than wood - the failure is very brittle. With the data collected, the fracture tendency could be explained.
New method developments receive excellent support from Shimadzu Innovation Center “Composites and Additive Manufacturing” in Duisburg, Germany. Active cooperation is the basis for successful joint developments to ensure the achievement of goals in scientific and economic projects. Shimadzu has a long-standing reputation in materials testing products and celebrated its 100th anniversary in 2017 as a leading supplier of analysis and testing systems in terms of technology, product and support, both in Japan and Europe.
For further information, see application news:
Prof. Dr.-Ing. Frank Walther
TU Dortmund University, Department of Materials Test Engineering (WPT)
Baroper Str. 303, D-44227 Dortmund, Germany
Website: https://wpt.mb.tu-dortmund.de/en/
Main Research Areas
Prof. Walther’s research career started with the studying of steels for high-speed railway wheel applications during his PhD, and expanded toward new characterization and measurement strategies for further steel grades and lightweight metals during his PostDoc qualification. His main research areas are the microstructure- and mechanism-based characterization and modeling of fatigue behavior, damage evolution and tolerance, (remaining) capability, and lifetime calculation of materials, aiming for a comprehensive quantitative process-structure-property understanding. Prof. Walther has published around 400 research papers (ORCID 0000-0003-2287-2099) and maintains close scientific contact with institutions and industries worldwide.
The Department of Materials Test Engineering (WPT) is headed by him, together with two senior engineers: Dr. Daniel Huelsbusch and Dr. Marina Macias Barrientos. There are four WPT research groups. These groups focus on 1./ Steels, led by Nikolas Baak, 2./ Light Metals, led by Alexander Koch, 3./ Composites, led by Ronja Scholz and 4./ Additive Manufacturing, led by Jochen Tenkamp. Research in all groups is geared toward determining the influence of processing (parameters) on microstructures and the resulting material properties to guarantee an application-optimized loading capability, safe operation conditions, and efficient product development based on an enhanced level of scientific knowledge. A microstructure is like the fingerprint of the properties, and current research focuses on characterization and modeling approaches for precise data acquisition. There are diverse applications in the automotive and aerospace, plant and power as well as biomedical engineering sector shaping the research being conducted.